Choosing and Maintaining Mining Chain Conveyors
- Share
- Issue Time
- Jul 9,2025
Summary
Selecting the right type of conveyor chain—especially the Drop Forged Chain—and maintaining it properly can significantly impact operational efficiency, safety, and cost-effectiveness.
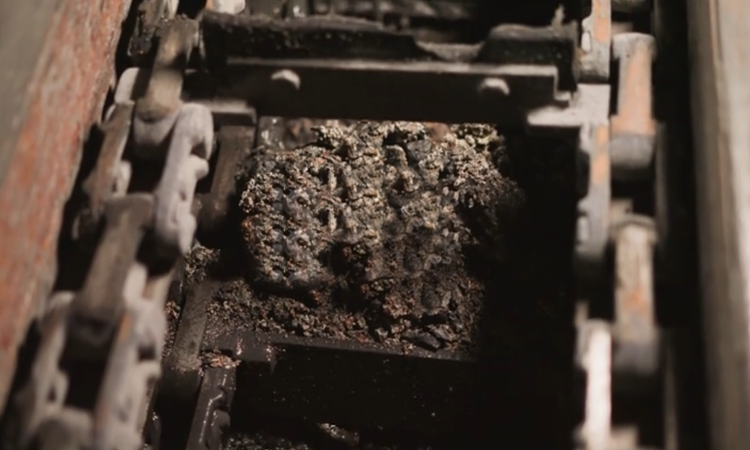
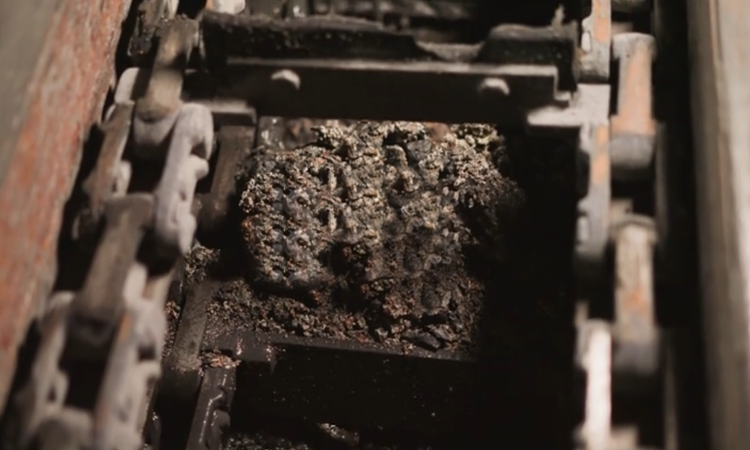
In the demanding world of mining, efficient material handling is critical. Mining chain conveyors play a vital role in transporting bulk materials such as coal, ore, and aggregates under harsh conditions.
Types of Mining Chain Conveyors
Chain conveyors come in various designs, each suited to specific mining applications. Common types include:
● Apron or Pan Conveyors:
Ideal for heavy-duty tasks, such as transporting large quantities of bulk materials like coal and ore. These can also operate in wet conditions for washing and drainage.
● Cross-Bar or Arm Conveyors:
Used for unit loads like drums or bags, often in automated systems.
● Drop Forged Chain Conveyors: Known for their strength and durability, these are especially suitable for high-load, abrasive environments.
Among these, Drop Forged Chains are particularly valued in mining due to their robust construction and resistance to wear and fatigue.
Selecting the Right Drop Forged Chain
As a professional conveyor chain manufacturer, CamelConvey recommends considering the following factors when choosing a Drop Forged Chain for mining operations:
● Material and Coating
Choose chains made from high-grade alloy steel for superior strength and wear resistance.
For corrosive or wet environments, opt for chains with protective coatings or stainless steel variants.
● Load Capacity
Evaluate the maximum load the chain will bear. Drop forged chains are ideal for heavy loads due to their high tensile strength and fatigue resistance.
● Operating Environment
Underground Mining: Requires chains with high resistance to abrasion and impact.
Open-Pit Mining: Look for chains that can withstand extreme temperatures and weather conditions.
High-Temperature Zones: Select heat-treated chains for applications like clinker or sintered ore transport.
● Chain Pitch and Design
The pitch must match the sprocket and conveyor system design.
Custom designs may be needed for steep inclines or curved paths.
● Maintenance Accessibility
Chains that allow easy inspection and replacement of worn links reduce downtime and maintenance costs.
Maintenance Tips for Long-Lasting Performance
Proper maintenance is essential to extend the life of your mining chain conveyor. CamelConvey suggests the following best practices:
● Regular Lubrication: Use high-quality lubricants to reduce friction and wear between chain links and sprockets.
● Routine Inspection: Check for signs of elongation, corrosion, or cracked links. Replace damaged sections promptly.
● Tension Adjustment: Maintain proper chain tension to prevent slippage and excessive wear.
● Clean Operating Environment: Remove debris and material buildup to avoid jamming and premature wear.
● Monitor Load Conditions: Avoid overloading the conveyor beyond the chain's rated capacity.
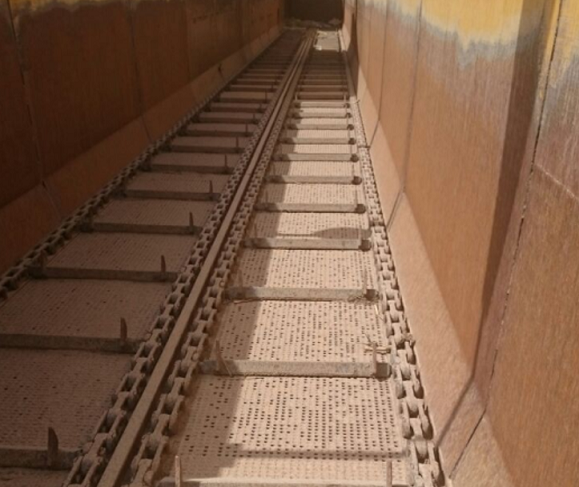
Choosing the right Drop Forged Chain for your mining chain conveyor is a strategic decision that affects productivity, safety, and operational costs. With expert guidance from CamelConvey, a trusted conveyor chain manufacturer, and a proactive maintenance plan, your conveyor system can deliver reliable performance even in the toughest mining environments.