Maximizing Automotive Manufacturing Efficiency with Overhead Power and Free Conveyor Systems
- Share
- Issue Time
- Jul 3,2025
Summary
Discover how overhead power and free conveyor systems revolutionize automotive production by enhancing throughput, flexibility, and space optimization—and how CamelConvey's components empower global integrators to excel in these solutions.

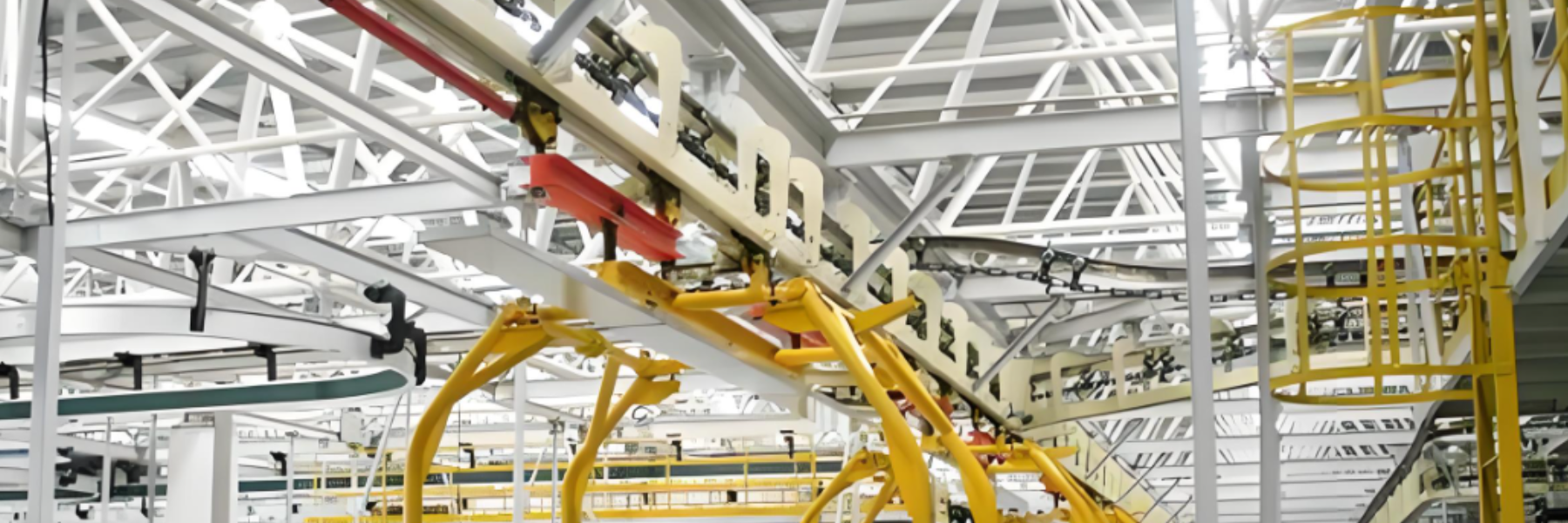
Overhead power and free conveyor systems stand at the forefront of modern automotive manufacturing, offering unmatched operational flexibility, efficient spatial utilization, and precise component handling. As an established global supplier of overhead conveyor parts, CamelConvey has supported top-tier system integrators by delivering high‑quality components that ensure reliability, modularity, and seamless integration.
What Makes Power and Free Conveyor Systems Ideal for Automotive Operations?
Automotive manufacturers demand conveyors that support varied process zones—painting, assembly, curing, storage—without halting entire lines. Power and free conveyors answer this need by separating power (continuous driven chain) and free (independent trolley motion):
- Trolleys latch onto or detach from the power chain as required
- Individual parts can accumulate, stop, or bypass without system-wide disruptions
- Ideal for paint shops, assembly branching, buffering, and routing across complex layouts
Flexible Flow and Precise Process Control
- Asynchronous trolley movement enables customized speed zones and timed processing
- Power line drives continuous motion; free line allows standstill at workstations without halting upstream flow
Space Optimization and Vertical Integration
- Overhead mounting moves heavy loads overhead, freeing floor space for personnel and machinery
- Enables multi-level layouts, vertical transitions, curves, and gradients
Industry Trends & Market Growth
Global power and free conveyor systems are projected to grow steadily—USD 1.2–1.5 billion market in 2024–25 with ~6–7% CAGR through 2030.
Key drivers include:
- Expansion of smart factory automation and lean manufacturing
- EV lines requiring precise handling of heavy modules
- Growth across Asia‑Pacific and e‑commerce logistics sectors
Market Landscape:
- Major players include Daifuku, Dürr, and Jervis Webb
- SME suppliers like CamelConvey specialize in fast, interoperable part solutions for integrators
CamelConvey's Competitive Edge in Overhead Power and Free Systems
As a trusted parts supplier since 1993, CamelConvey delivers high-performance overhead conveyor components tailored for automotive integrators:
Comprehensive Product Range
- Includes I‑beam rails, enclosed‑track chains, drop‑forged rivetless chains, trolleys (2″–6″), attachments, and full power and free kits
- Engineered to withstand heavy loads, high temperatures, and corrosive conditions
System Compatibility & Modularity
- Designed to integrate seamlessly with major brand systems (e.g., Webb, Daifuku)
- Modular design allows flexible zoning, line expansion, and system retrofitting
Quality, Reliability & Support
- Forged-steel trolleys with hardened bearing wheels reduce maintenance cycles
- Precision 40Cr chains ensure durability and smooth operation
- Global delivery and technical support for system integrators
Real-World Use Cases for Automotive Integrators
1.Paint Shops & Curing Ovens
CamelConvey's corrosion-resistant components and heat-tolerant trolleys perform flawlessly under high-temperature operations.
2.Assembly & Branching Lines
Free-track trolleys enable dynamic diverging/merging across assembly zones without stopping conveyors.
3.EV Battery & Powertrain Handling
Heavy-duty chains and roller trolleys handle EV battery packs and engine modules, while modular layouts adapt for future vehicle platforms.
Best Practices for Implementing Power and Free Systems
1. Design for Flexibility: Use dual tracks and branch lines to support multiple workflows.
2. Select High-Precision Components: Choose trolleys and chains rated for specific load and environmental demands.
3. Plan for Maintenance & Lubrication: Use sealed wheels and treated tracks to minimize downtime.
4. Build for Modularity: Adopt interchangeable parts for line expansion and system upgrades.
CamelConvey offers full engineering support, sample delivery, and technical consultation for efficient system integration.
Partnering with CamelConvey: Why It Matters
1. Expertise: Over 30 years of experience supplying key parts to global integrators ensures technical alignment and system reliability.
2. Agility: No minimum order quantity (MOQ), fast prototyping, and on-time delivery give OEMs and integrators the speed they need.
3. EEAT‑Driven Trustworthiness:
- Experience: Global deliveries and diverse automotive use cases
- Expertise: Broad portfolio of overhead conveyor components
- Authoritativeness: Engineered compatibility with major systems
- Trustworthiness: Proven reliability and customer confidence
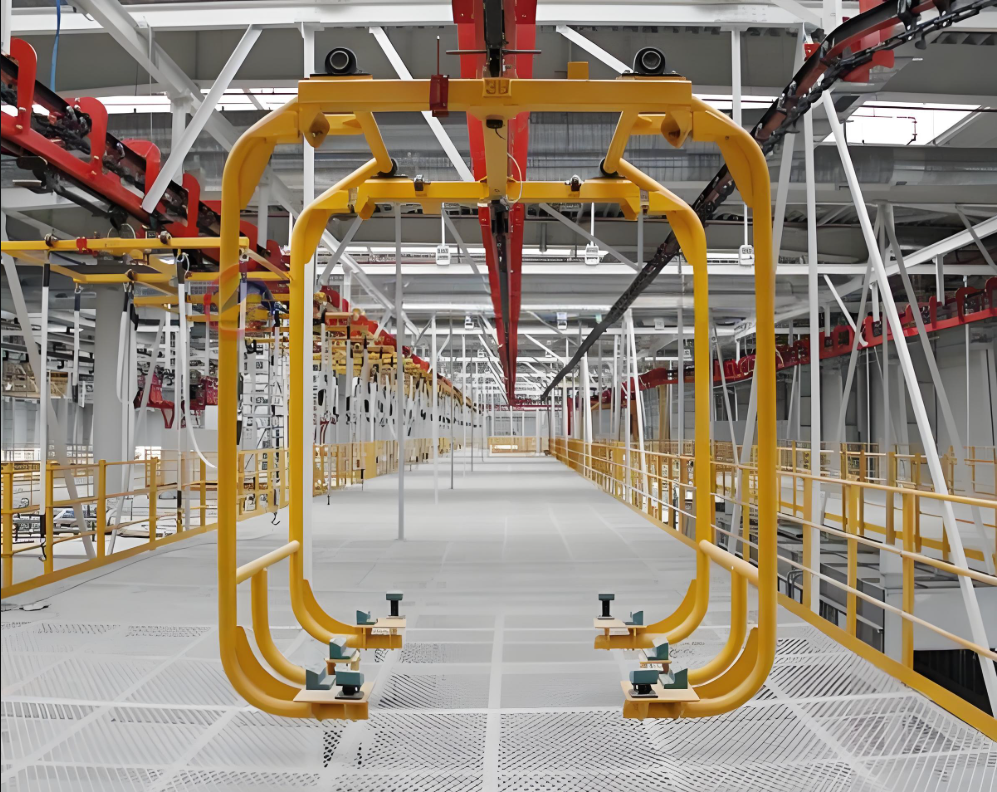
Power and free conveyor systems are essential to future-ready automotive manufacturing—offering autonomy, flexibility, vertical efficiency, and scalability for electric vehicle production. As a trusted supplier, **CamelConvey** empowers integrators with premium, compatible components supported by deep technical experience and global fulfillment.
- Power and free systems offer advanced routing, zoning, and buffering for complex automotive processes.
- Market growth is driven by automation and EV production.
- CamelConvey delivers dependable, interoperable, globally supported parts.
- Partner with CamelConvey to future-proof your conveyor infrastructure.