Types of Material Handling Systems and Their Industrial Applications
- Share
- Issue Time
- Dec 20,2024
Summary
This article will explore how to choose the right material transportation system, the advantages of modular design and installation, and methods to improve material handling efficiency.
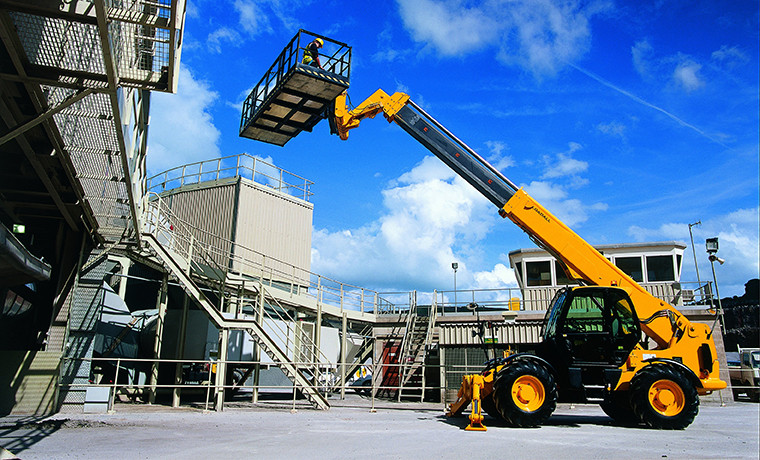
In modern industries such as agriculture and warehousing, the choice of material handling equipment plays a crucial role in production efficiency and operational costs. Whether it's for material handling, stacking, or transportation, efficient and reliable equipment systems are essential.
How to Choose the Right Material Handling Equipment?
There is a wide variety of material handling equipment, including agricultural conveyor chains, forklifts, stackers, automated guided vehicles (AGVs), and more. When selecting the appropriate equipment, several key factors need to be considered:
1. Material Type:
Different types of materials require different handling equipment. For example, common agricultural materials such as crops, seeds, and fertilizers are typically in bulk, bagged, or loose forms, while warehouse materials often include boxed goods, pallets, and standardized items. Understanding the characteristics of the materials—such as their shape, size, and weight—helps determine the most suitable equipment. For instance, an agricultural conveyor chain is ideal for bulk handling, while a box conveyor may be better for standardized items in a warehouse setting.
2. Transport Distance and Space Layout:
Different equipment suits different transport distances and space configurations. Short-distance transport can utilize manual forklifts, stackers, or simple conveyor belts, while long-distance, high-efficiency transport requires automated systems, such as AGVs or advanced conveyor systems. Additionally, it's important to consider the warehouse layout to ensure the equipment can operate efficiently in the available space.
3. Cost and Return on Investment:
The initial investment is a significant factor when selecting material handling equipment. Although some automated systems have a higher upfront cost, they can significantly increase productivity and reduce labor costs in the long run. By evaluating the total cost of ownership and long-term operational expenses, businesses can choose the most cost-effective solution to achieve a higher return on investment (ROI).
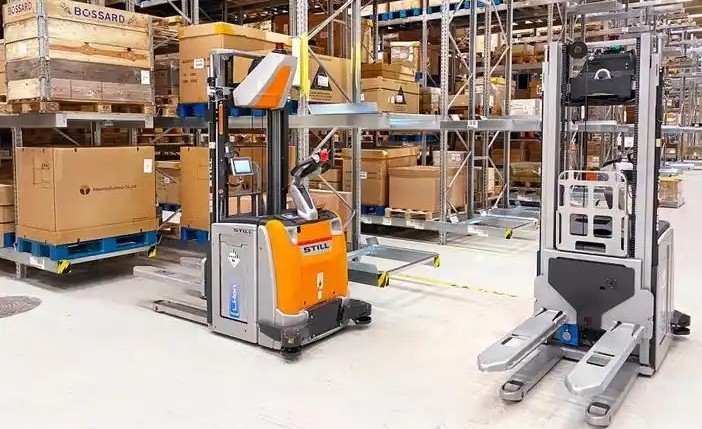
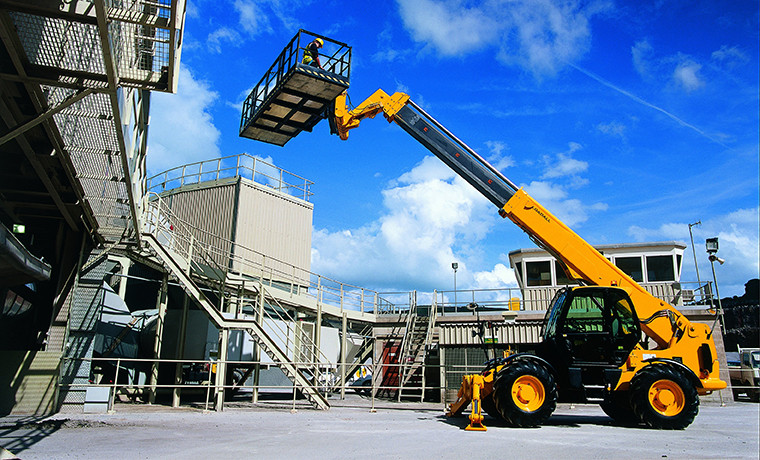
The Advantages of Modular Design and Installation for Material Handling Systems
Modular design for material handling systems is becoming increasingly popular, especially in large-scale warehousing and agricultural production. Modular design means that the system's components are designed, manufactured, and installed independently and can be flexibly combined according to needs. This design approach offers several advantages:
1. Flexibility and Scalability:
Modular systems allow users to select and combine different modules based on their requirements, enabling easy system expansion or modification. This is especially beneficial for businesses that need to gradually scale their operations, as they can add more equipment or improve system efficiency without major changes to the existing infrastructure.
2. Lower Maintenance Costs:
Since modular equipment is easy to disassemble and replace, maintenance becomes more efficient. In the event of a failure, only the affected module needs to be replaced, rather than the entire system, thus reducing downtime and maintenance costs.
3. Faster Installation and Deployment:
Modular design makes installation simpler and faster. By pre-manufacturing the components of the system in a factory, installation at the site only requires assembly, significantly reducing deployment time. This enables businesses to quickly enhance their material handling efficiency.
Methods to Improve Material Handling Efficiency
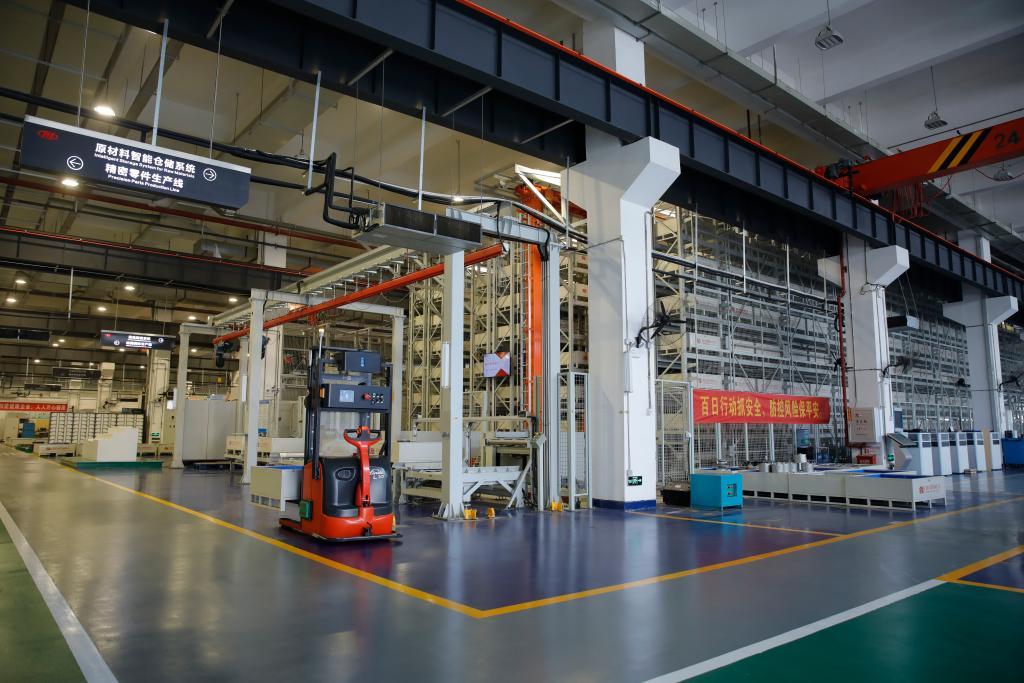
Automated Systems
With technological advancements, more and more businesses are adopting automated material handling equipment. Automated guided vehicles (AGVs), advanced conveyor systems, and smart warehousing systems can greatly improve material handling efficiency. These systems reduce human intervention and optimize routing, resulting in faster and more accurate material handling.
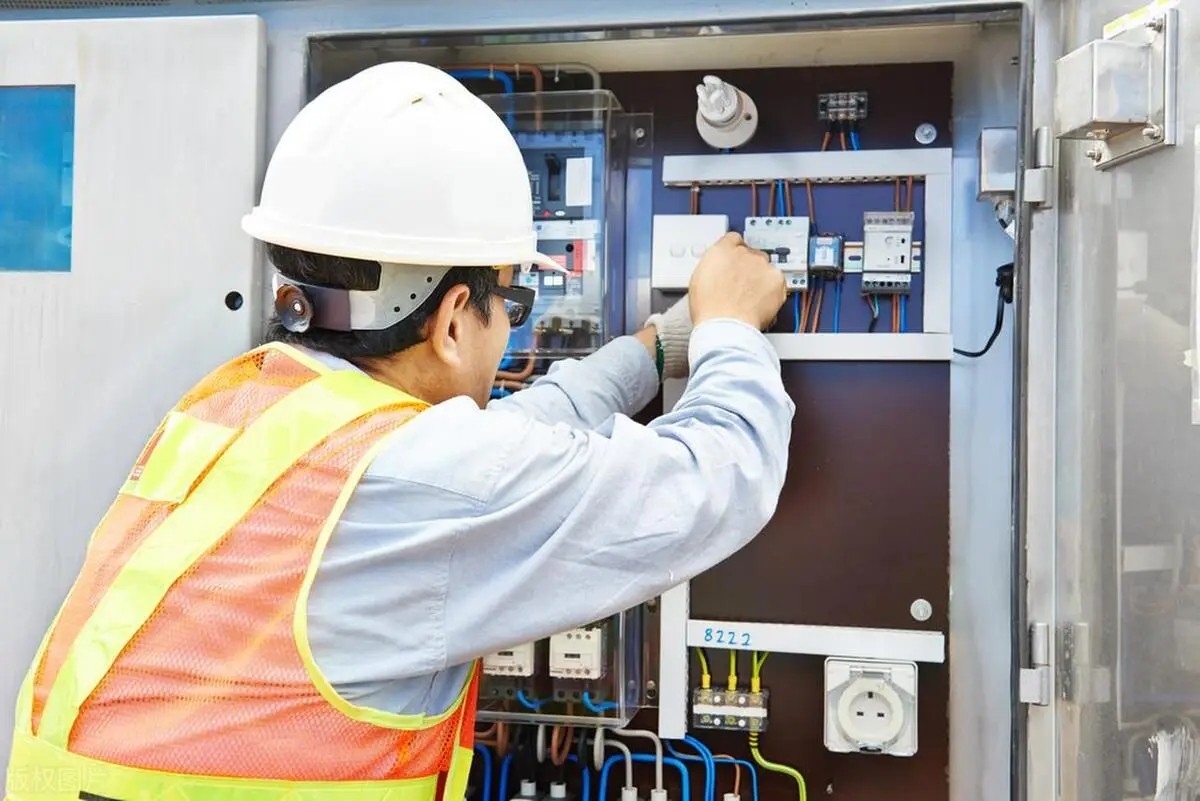
Regular Equipment Maintenance
Regular maintenance and servicing of material handling equipment are essential for ensuring optimal performance. By performing regular inspections of critical components such as motors, drive systems, and sensors, businesses can identify potential issues early and prevent breakdowns that could disrupt operations.
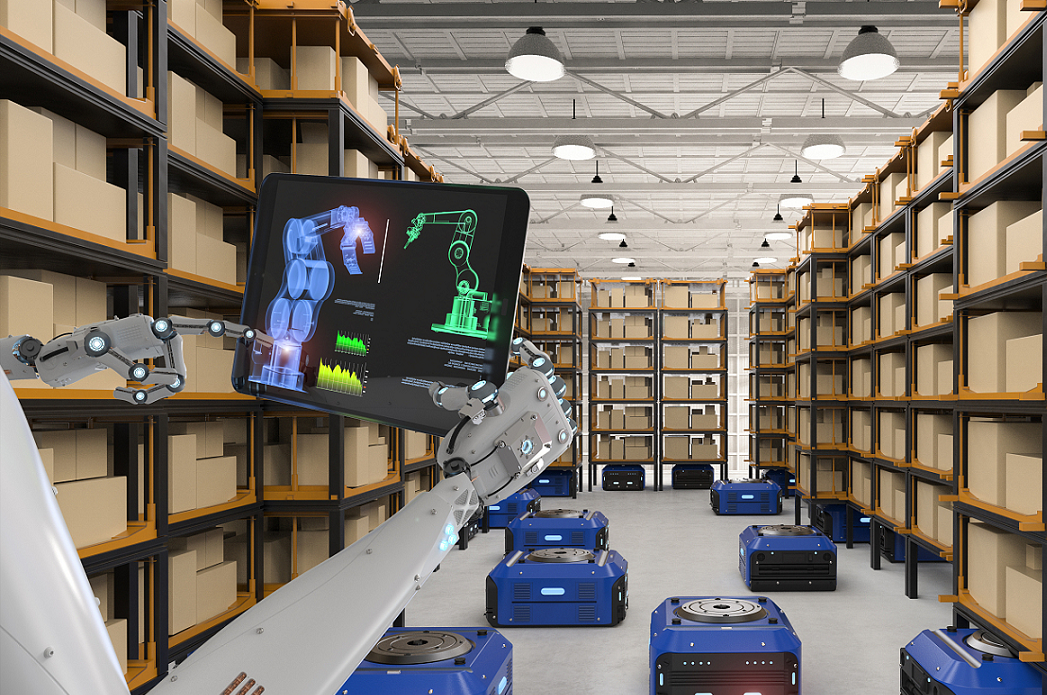
Intelligent Scheduling Systems
Implementing intelligent scheduling systems can help businesses better manage their material handling operations. These systems use real-time data (such as arrival times and transport requirements) to optimize material handling routes and task assignments, improving system efficiency and equipment utilization.
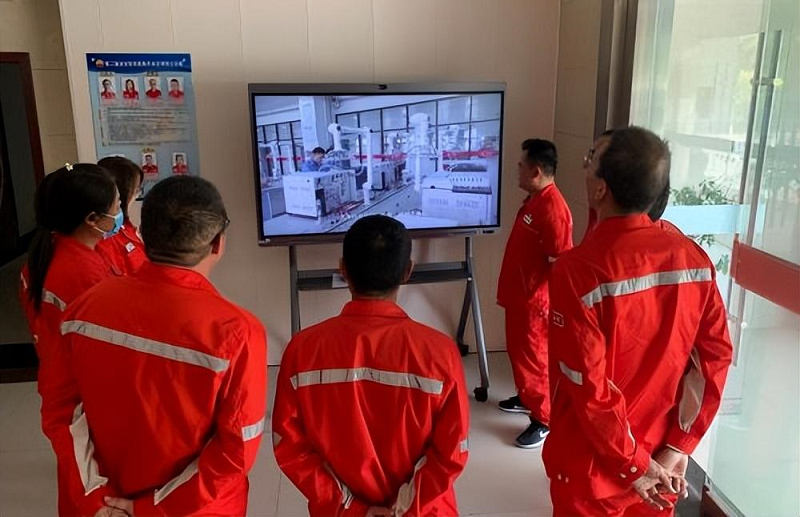
Employee Training
Proper employee training is crucial for ensuring that operators understand the equipment's functions and best practices. This reduces errors, improves safety, and boosts overall efficiency. By enhancing employees' skills and safety awareness, businesses can prevent costly mistakes and increase productivity.
Case Studies
A traditional sugar cane factory faced efficiency challenges, relying on manual labor and outdated machinery for transporting cane. During peak seasons, this led to delays and production bottlenecks.
To improve, the factory implemented a SUGAR MILL CHAIN system, specifically designed for farm products. The new agricultural conveyor chain reduced transportation time, minimized delays, and handled larger loads without breakdowns.
As a result, production efficiency increased by 30%, costs dropped, and the operation became more stable and automated. This shift demonstrated how adopting modern technology can significantly enhance efficiency in traditional industries.
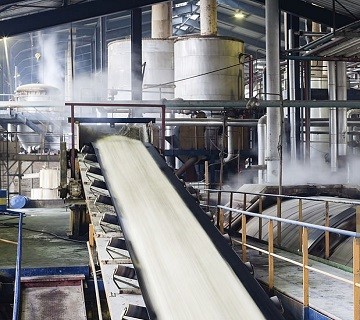
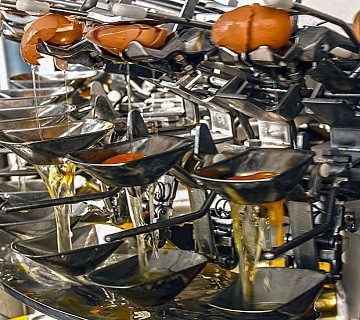
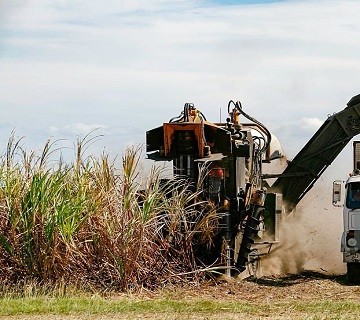
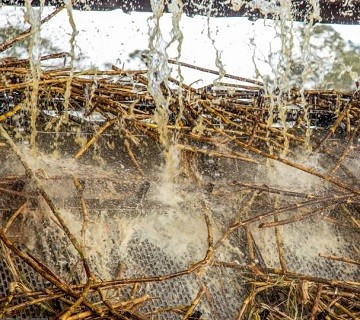
Choosing the right material handling equipment, optimizing system design, and improving handling efficiency are key factors for businesses in agriculture, warehousing, and other industries to stay competitive. By selecting suitable equipment, leveraging modular design, implementing automated systems, maintaining equipment regularly, and investing in employee training, companies can significantly improve production efficiency while reducing operational costs. With ongoing technological advancements, the future of material handling systems will be more intelligent, flexible, and efficient, driving major industry transformations.