Optimizing LPG Bottling Operations: Dry vs. Wet Conveyor Chain Systems
- Share
- Issue Time
- Jul 16,2025
Summary
The selection between dry and wet conveyor chain systems represents a critical decision point for LPG bottling chain plant operators
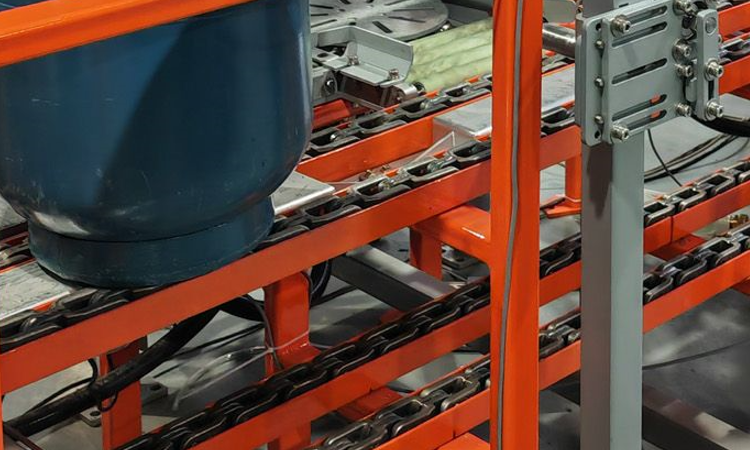
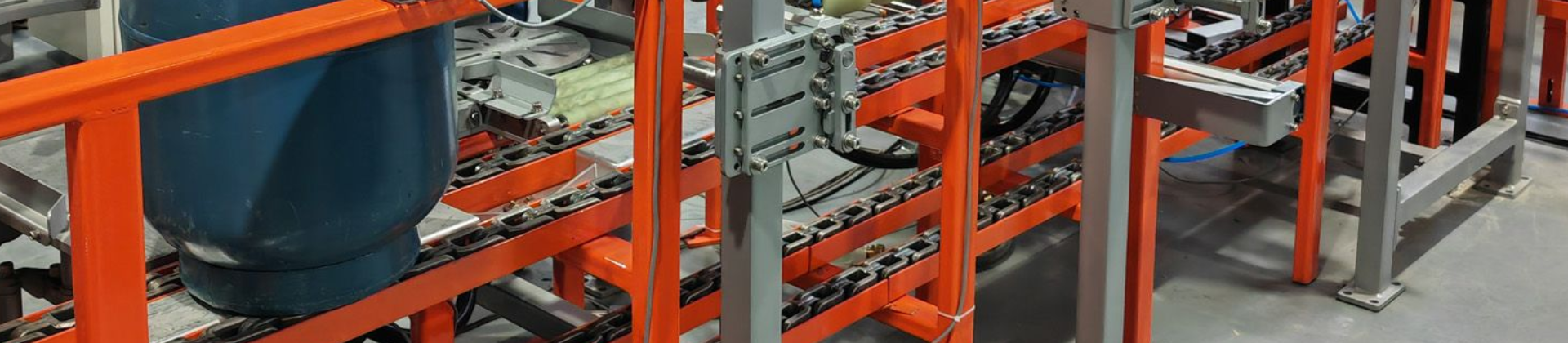
The selection between dry and wet conveyor chain systems represents a critical decision point for LPG bottling chain plant operators, directly impacting operational efficiency, maintenance requirements, and long-term cost structures. As industry leaders in conveyor solutions, Camelconvey present this technical comparison to guide your equipment selection process.
Technical Overview
Modern LPG bottling facilities primarily utilize two chain system configurations:
1. Wet-running chains (CC600 case conveyor chain and F801 case conveyor chain)
2. Dry-running chains
Each configuration demonstrates distinct performance characteristics that must be carefully evaluated against operational parameters and environmental conditions.
Wet-Running Chain System Analysis
The CC600 chain and F801 wet-chain system employs a specialized black soap/grease emulsion lubrication system, delivering:
Operational Advantages:
● Enhanced wear reduction (up to 40% longer service life vs. unlubricated systems)
● Intrinsic spark suppression for ATEX compliance
Maintenance Considerations:
● Requires daily lubrication system checks
● Weekly deep-cleaning protocols recommended
● Quarterly track inspection intervals
● Annual chain replacement typical in continuous operation
Dry-Running Chain System Performance
Our advanced dry-chain systems utilize engineered polymers
Operational Benefits:
● 60% reduction in routine maintenance labor
● Elimination of water consumption (ideal for arid regions)
● Simplified ancillary systems (no pumps/mixers required)
Performance Trade-offs:
● 15-20% faster wear rate than wet systems
● Higher initial material costs (offset by reduced maintenance)
● Requires precision alignment for optimal performance
Selection Methodology
The optimal chain system depends on key operational factors:
For wet systems consider:
● Water availability and treatment infrastructure
● Explosion protection requirements
● Production volume demands
For dry systems evaluate:
● Water conservation priorities
● Maintenance crew availability
● Capital vs. operational expenditure balance
The choice between dry and wet conveyor systems represents a strategic investment decision that will impact your operation for years to come. CamelConvey technical team stands ready to assist in selecting and implementing the optimal solution for your specific operational requirements.
CamelConvey F801 case conveyor chain stand out due to their robustness and high performance.
CamelConvey CC600 case conveyor chain is engineered to meet the highest standards in performance and durability.
DF3500 chain's versatility allows it to be used in a wide range of industries,such as bottling,packaging and case management.
MC33 Double Flex Chain is a versatile and reliable conveyor chain that can be used in a wide variety of applications.